The Role of LSR Molding in Medical Device Manufacturing
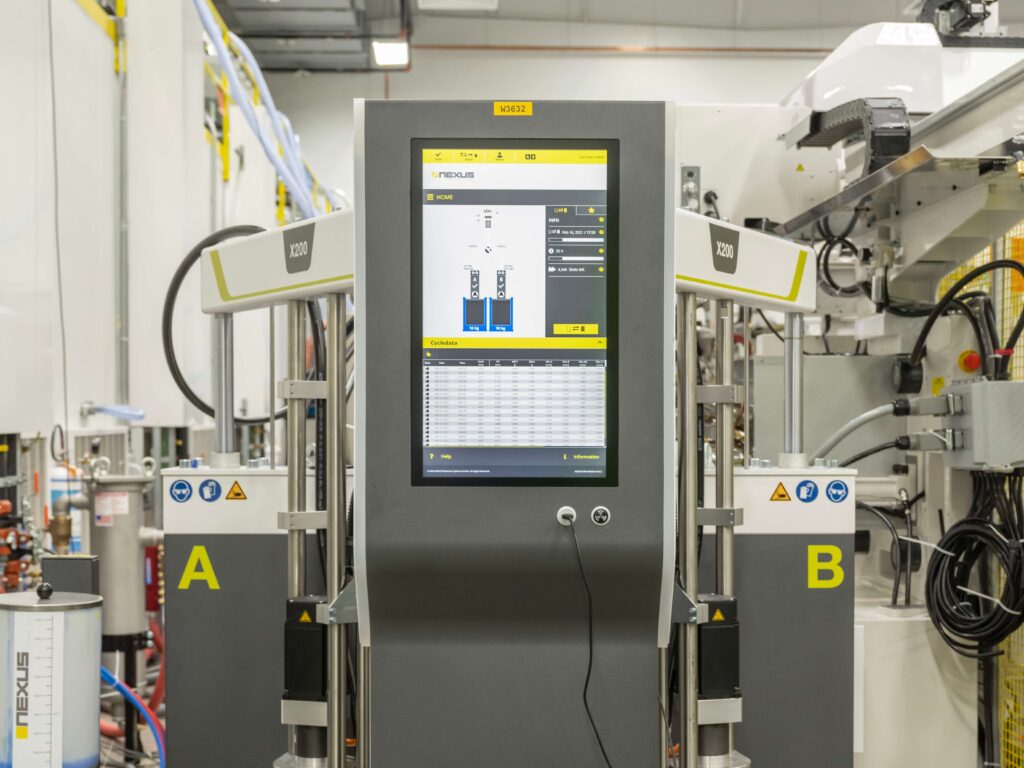
The 2020 COVID pandemic was a catalyst for growth for medical devices, as it displayed how this industry can be used to improve patient outcomes, quality of life, and healthcare processes. The medical device market is projected to hit a global revenue of $595 billion in 2024, and this will only further advancements in this industry. However, these advancements and exponential growth will only raise the demand for precision, reliability, and biocompatibility in medical device manufacturing.
Liquid silicone rubber (LSR) has become essential in addressing these needs, offering biocompatibility, precision, and FDA compliance. LSR is an inorganic polymer made of silicon, oxygen, carbon, and hydrogen. Its fundamental structure is made up of siloxane, which is oxygen and silicon. This unique combination offers high flexibility and durability.
Why Medical-Grade Liquid Silicone Rubber is Ideal for Medical Devices
Medical-grade liquid silicone rubber has become popular due to its inherent properties like biocompatibility and chemical inertness. Chemical inertness means it doesn’t react with other substances, particularly oxidation. This helps ensure its safety for medical devices and implants. Its exceptional resistance to chemical and thermal degradation also distinguishes it from other elastomeric materials that are being used in the industry, like rubber.
Biocompatibility
Biocompatibility is the ability of a material to safely interact with living tissues without causing adverse reactions. It is typically defined as “the ability of a material to function effectively while eliciting an appropriate host response in a specific application.” This implies that the material should not induce adverse reactions, such as toxicity or rejection when introduced into the body.
LSR is inherently biocompatible due to its chemical makeup and production process. This is crucial when choosing materials for devices that interact with human tissue.
FDA Approval
Medical-grade liquid silicone rubber’s biocompatibility also lends to its status as an FDA approved material for use in medical devices and even in packaging for some pharmaceuticals. LSRs have a wide temperature range from -58°F to 392°F, making them suitable for parts and devices intended to be inserted into the human body. LSR will remain flexible when exposed to low temperatures of around -50°F without becoming brittle and hard. This stays in line with the Code of Federal Regulations that all FDA-approved silicone must adhere to.
Ready to discover if LSR is the right choice for your product? Contact Tessy today to get started!
The Role of LSR Molding in The Manufacturing Process
Manufacturing medical devices requires precision to ensure safety and effectiveness, especially for biocompatible medical-grade liquid silicone rubber components. Even minor defects can have serious consequences. LSR molding is essential to meet these stringent standards:
Precision Molding
Liquid silicone rubber molding uses advanced molds and injection molding techniques to create components from biocompatible silicone rubber. This precise process ensures that all dimensions and specifications of medical devices are met accurately.
Design for Manufacturing (DFM) and high precision are critical when designing LSR molds. Using advanced software like Moldflow® and SIGMASOFT®, engineers can create virtual mold models and simulate the entire molding process, enabling control over critical factors such as temperature, automation, and venting, which affect the final part or product dimensions.
Reducing Defects
A key benefit of LSR molding is reducing defects and variations in the final product. By spotting potential issues early on during the process of liquid silicone rubber molding, engineers can adjust designs and optimize production parameters.
Tessy’s engineers efficiently develop and refine various prototype designs, saving time and quickly identifying acceptable and exceptional features. This proactive approach minimizes scrap rates and ensures all components meet high-quality and regulatory standards.
This is important in biocompatible liquid silicone rubber molding, as minor dimensional variations can greatly affect device functionality.
Accelerating Time-to-Market
Liquid silicone rubber molding boosts production efficiency with automated processes, reducing reliance on manual labor. This speeds up component production while maintaining quality, enabling employees to focus on other tasks.
The integration of cold runner technology in liquid silicone rubber molding reduces material waste, leading to cost savings and eliminating the need to trim excess material, thus improving manufacturing efficiency.
LSRs cure faster than many materials, with heat or pressure further speeding up production. Unlike other materials, liquid silicone rubber doesn’t need post-baking, saving both time and cost.
In rapidly evolving industries like automotive and electronics, LSR molding provides a key advantage by helping companies meet tight deadlines and quickly respond to market demands.
Rapid design prototyping also offers a key advantage for liquid silicone rubber molding by significantly reducing time-to-market for new products. Unlike traditional prototyping, which involves lengthy and costly development processes, rapid prototyping allows design teams to quickly create and test multiple product iterations. This leads to faster feedback and refinements, resulting in efficient product design turnarounds.
Rapid development is the name of the game, and no other LSR manufacturer does it better than Tessy. Contact us today to find out how we can accelerate your product’s time to market.
Key Benefits of Using LSR for Medical Devices
LSR is a versatile material known for its durability, chemical resistance, and biocompatibility. Here are some key benefits of using LSR in medical device development:
Durability & Flexibility
Liquid silicone rubber is known for its outstanding durability and flexibility. The hardness level of LSR plays a significant role in determining its properties. Various shore hardness levels are available, and LSR can be categorized from soft to hard.
Soft LSR, which features a lower shore hardness, is typically used in applications that require flexibility and elasticity, such as catheters, respiratory masks, and silicone implants. Medium shore hardness LSR provides a balance between flexibility and strength, making it suitable for products like gaskets, seals, and tubing utilized in medical equipment. Hard LSR, characterized by a higher shore hardness, is suitable for applications that demand rigidity and resistance to wear and tear. It is essential to select the appropriate shore hardness level to ensure that the LSR product meets the specific requirements of its intended application.
Liquid silicone rubber’s remarkable flexibility and elongation properties enable it to stretch without losing integrity, making it perfect for devices that undergo frequent movement or bending. The exceptional tear and tensile strength of LSR provides excellent resistance to deformation and tearing, greatly extending the lifespan of medical devices made from it.
Chemical Resistance
A major consideration in choosing materials for medical devices is their resistance to chemicals and sterilization. LSR is chemically inert, enhancing its biocompatibility and making it a safe choice for medical applications. It also offers excellent compatibility with various chemicals in comparison to other rubbers, including diluted inorganic acids and bases like acetic and sulfuric acid. This makes LSR appropriate for use in medical devices that may encounter these substances.
LSR’s exceptional resistance to chemicals, steam, and radiation also makes it ideal for medical devices that require regular sterilization, such as surgical instruments and implants. Its chemical resilience ensures it remains non-reactive with medications and bodily fluids, enhancing safety in medical applications.
Overall, LSR delivers incredible advantages in medical device manufacturing compared to more traditional elastomers like rubber. If you’re ready to find out more about whether this material is right for your product, contact Tessy. Our skilled team will help determine the best material choice for your needs– all you have to do is get started.