Advanced Research & Development for Product Innovation
What Has R&D Been Up To?
We know that innovation requires hard work and expertise, and we channel this into our dedication to creating groundbreaking solutions. Here are some ways our skilled R&D team has been working to advance our capabilities.
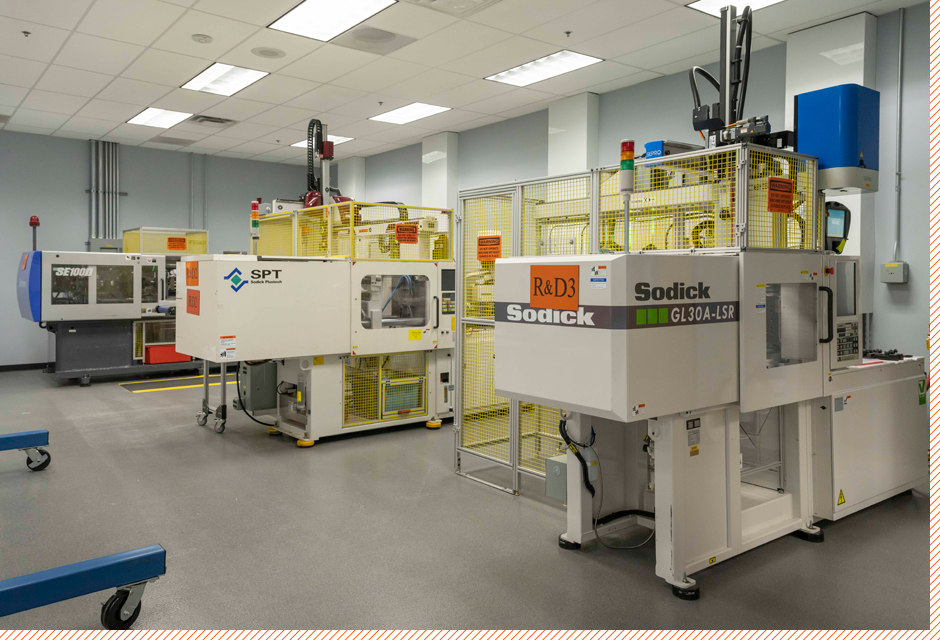
Proprietary Processes for Rapid Assembly
Our team developed and implemented Tessy proprietary laser welding processes utilizing enhanced optics combined with custom mirrors to weld multiple assemblies simultaneously on a high speed 150 part-per-minute medical assembly line, leading to improved cycle times and dramatically reducing the quantity of laser systems and labor required for the given cycle time.
Advancements in Microfluidic Flow
The research and development team enhanced the performance of microfluidic medical devices with a combination of precision molding, Tessy proprietary ultrasonic processing, and the utilization of precision tool manufacturing for high precision micro-channels to sub .002” accuracy followed by ultrasonic processing to .0005” accuracy as required.
Innovations in Polycarbonate Forming
The Tessy team developed a proprietary ultrasonic forming process for generic polycarbonate materials, eliminating assembly components, post processing operations, and the requirement for higher cost custom blended polycarbonate materials.

Pushing New Boundaries in Medical Product Testing
Many medical products require mass flow, pressure decay, and other means of critical product testing. Tessy has deployed Cincinnati Test Systems’ Blackbelt Pros as standard test equipment, offering superior test capability. The R&D team integrates CTS devices into manual and semi-automated test platforms, performing multiple tests to a single assembly providing rapid testing.
Fewer Failures, Swifter Success
Our team developed Tessy proprietary micro-assembly cells to drive automation advancements in tandem with in-process automation builds. These cells drive process development and identify processes or design issues early, saving customers’ capital and critical product launch milestones.
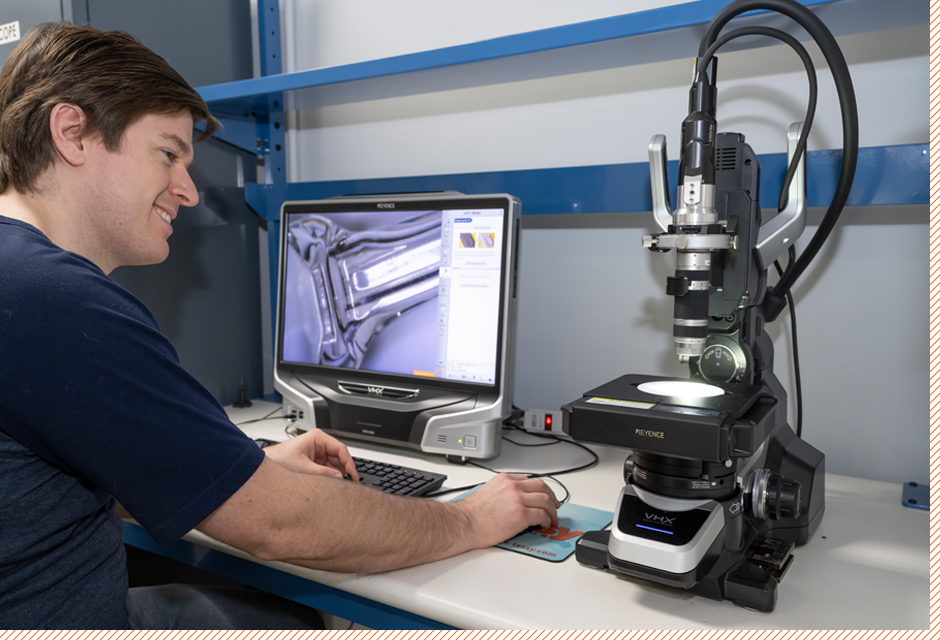
Spearheading Sustainability with Recyclable Resin
Tessy developed technology to blend ratios of post-consumer resin and virgin material to deliver a recycled product that does not require tooling changes. We accomplished this by identifying ways to purify PCR while maintaining material properties and utilizing the recycled resin across a multitude of applications – ultimately keeping the recycling loop continuous.
Making Plastics Better for The Planet
Our research and development team also created resins that emulate physical properties of Polypropylene (Homogenous and Co-Polymers) as well as Low Density Polyethylene to produce biodegradable products.
What can we do for you?
Contact Tessy to find out how our capabilities can be– or create– the answer you’ve been looking for.
Research & Development Tools and Equipment
Leveraging advanced tools and machinery is instrumental to Tessy’s success in creating truly innovative solutions to complex manufacturing issues. These are just a few of the tools used by our research and development team to transform roadblocks into opportunities:
Prototyping
- SLA 3D Printers
- FDM 3D Printers
- Polyjet Multi-material & Color 3D Printer
- 5-axis CNC Milling Machine
- Lathe
Testing
- Environmental Chamber
- 3D Microscope
- Camera Vision System
- Tension/Compression Force Testers
- Material Moisture Analyzer
Molding
- Molding Machines
- LSR Machine
Assembly
- Flex Feeding Systems
- Ultrasonic Welder
- Laser Welder
- Laser Marker-Engraver
- Direct Part Printing
- Label Application
- In-mold Labeling
- Spring Feeding Systems
- Heat Stake Machine
- Soldering-Electronics Workstation
- Liquid Dispensing Station
- Flame/Plasma Treaters
Interested in our research and development capabilities?
We want to hear from you! Contact Tessy today to get started.