The Rise of Micro Molding in Miniaturized Medical Devices
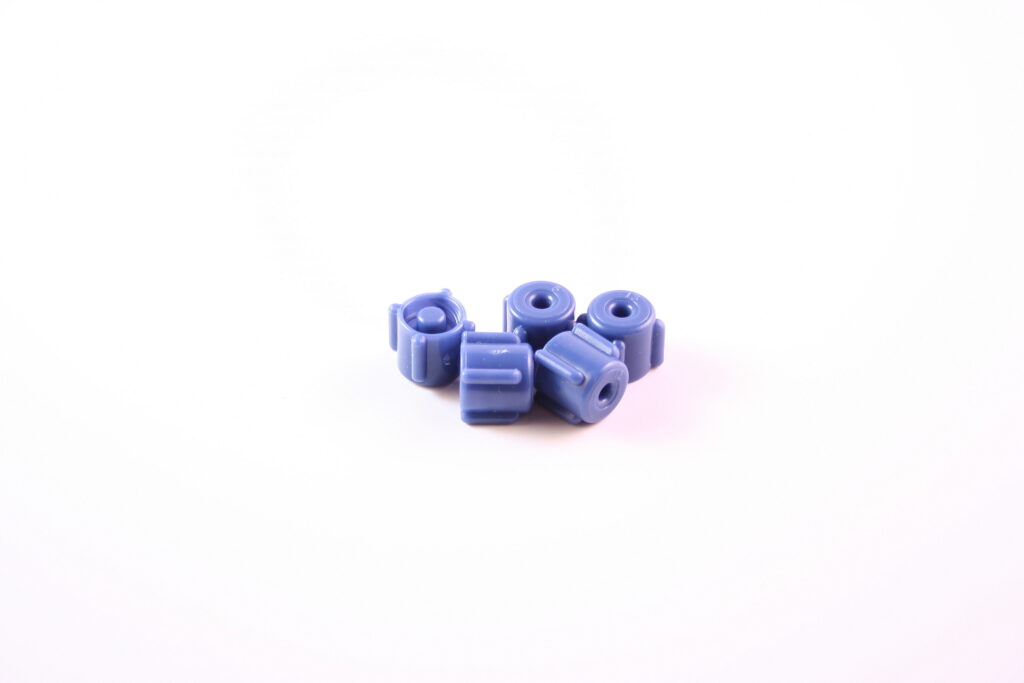
Every player in the medical device manufacturing industry is always looking for the next big thing, but what about the small breakthroughs– literally? As medical technology continues to advance, parts are getting tinier, tolerances are getting tighter, and diminishing lead times are becoming favored more and more. Though these challenges may loom large for medical product development, one solution comes in a smaller package than you might imagine: enter micro molding.
Micro Molding Defined
Micro molding is just what it sounds like: molding plastic materials into parts and products on a smaller scale. Modeled after traditional injection molding and sometimes referred to as ‘micro injection molding’, this process takes the same tools and principles and scales them down. Where a traditional injection molding machine may exert thousands of pounds of clamping force on its tools, a micro injection molding machine typically exerts less than a hundred during each cycle. And where injection molding tools can create parts that are greater than a foot in width, micro molding accommodates parts that are less than a fraction of an inch across. So, why scale back? The truth is that working with less actually empowers manufacturers to do so much more when creating miniature parts for the medical devices that improve people’s everyday lives. Here’s what micro molding can do.
Revolutionizing Medical Device Production With Micro Injection Molding
While micro molding may use similar equipment to injection molding, it’s anything but a 1:1 equivalent. Just as traditional injection molding can churn out parts that are impossible to make with micro molding, the opposite is also true. Micro injection molding allows for the creation of parts that are measured in microns, with features small enough to be imperceivable to the naked eye. On this scale, plastics and resins behave differently than they would under normal conditions, in some cases even surpassing the material’s intended specifications. Parts that are normally deemed “impossible” become not just possible, but achievable through careful DFM including mold design and material selection. It’s worth noting that not all micro molded parts are microscopic themselves. Parts that can be seen without visual aids (typically with dimensions of half an inch or less) that are designed to have microscopic features would also be considered micro molded parts.
Mold Tooling: Save Big With Smaller Molds
Micro injection molding tools are significantly smaller and thinner than their traditional counterparts. This offers many advantages at both the tooling and manufacturing stages. With less material to work with, micro molds can be created much faster (and often cheaper) than full sized molds, although they do require specialized machines to be created. Machines and methods like micro mills, electrical discharge machining (EDM), and wire EDM are some of the most common. During the manufacturing stage when these molding tools actually get used, their small size allows for greater control over the mold’s temperature as there’s less surface area and volume to manage. This matters because greater temperature control during the molding process can help with creating finer part details and achieving maximum cavitation per shot.
Where Are Micro Molded Parts Used?
Speaking of parts, what exactly can micro injection molding make? These are just a few examples:
- Gears
- Connectors
- Housings
- Wheels
- Bearing retainers
- Lenses
- Clips
- Straws
- Electronic enclosures
Keep in mind that each individual piece can be produced to dimensions of 100 microns or less, with tolerances just a fraction of the size of a human hair. These tiny parts are used in wearable end products like hearing aids, implantable products like pacemakers, pharmaceutical delivery products, and everything in between. This means that each part must meet otherwise unseen levels of precision, leading us to…
The Challenges of Micro Molding
Successfully creating accurate and precise parts on a micro scale is no small feat. With micro molded parts seeing end use in devices that transform the lives of countless people for the better, it is absolutely crucial that they meet exacting tolerances to perform exactly as anticipated. Two of the most significant challenges come in the form of meeting dimensional tolerances as designed, and understanding how material behavior can impact the production and quality of the final parts.
Meeting Dimensional Tolerances
This method takes precision manufacturing to new extremes. Where most injection molded parts are graded on a pass/fail basis in measurements of millimeters, micro molded parts are measured on a scale 1,000 times less forgiving. Meeting these tight tolerances requires careful attention to detail when engineering and machining molds.
Material Behavior
As previously mentioned, materials don’t behave quite the same when you’re working on such a small scale. In fact, many flow simulators will simply not return accurate results on micro molded part designs– if they return any results at all, that is. At such small quantities, materials flow and fill differently than you may expect to see in a traditional injection molding process. This can be something of a double edged sword. A thorough understanding of how a material’s behavior and its properties both change in micro injection molding is critical to selecting the right plastic or resin for the application at hand.
You don’t have to play the guessing game. Rely on Tessy’s expertise in materials for your micro injection molding needs.
Traditional vs. Micro Injection Molding
Now, all of this isn’t to say that traditional injection molding is better than micro injection molding or vice versa. Both types have their use cases which are largely dependent on the production scale of the project and the dimensions of the final part. Below is a table that compares the two to help you narrow down which method might be better for your needs.
Capabilities | Injection Molding | Micro Molding |
Part Size | > 1 in. | < 1 in. |
Manufacturing Volume | High Volume | Low to High Volume |
Shot Volume | > 1 oz. | < 1 oz. |
Dimensional Tolerance | 150μm ≤ x ≤ 30μm | x ≥ 0.5μm |
With these new and exciting possibilities in mind, you may be wondering how you can begin to harness the advantages of micro injection molding. The easiest way to get started is to connect with the medical manufacturing experts at Tessy!
Micro Molding Done Right at Tessy
As specialists in all things medical device manufacturing, Tessy is equipped with micro injection molding capabilities at multiple locations across the nation. Some highlights of our capabilities include the following:
- 40+ micro injection molding machines across all locations
- Ability to mold tolerances down to .0005mm total and +/- .001mm routinely
- Shot weights as small as .07 oz.
- Horizontal and vertical molding
- Micro press integration into automated assembly equipment
- Insert over molding
Ready to learn more about what we can do for you? Contact Tessy today to take the first small step toward micro manufacturing success.